Why high-reliability power management is essential for aerospace, defense, and space systems
Power management modules are the unsung heroes of mission-critical electronics, ensuring stable and efficient operation in extreme environments. This post highlights how innovations in wide-bandgap semiconductors, radiation-hardened power supplies, and smart power distribution systems are enhancing reliability and performance.
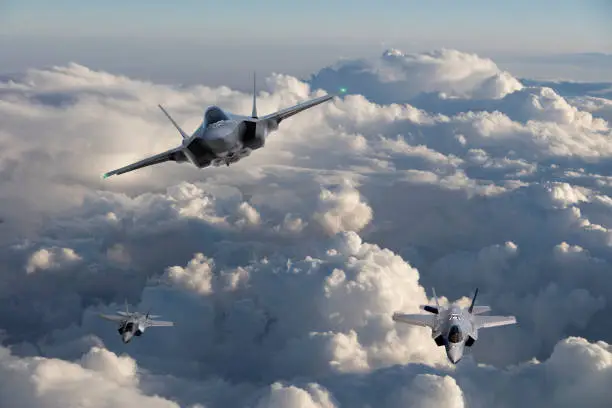
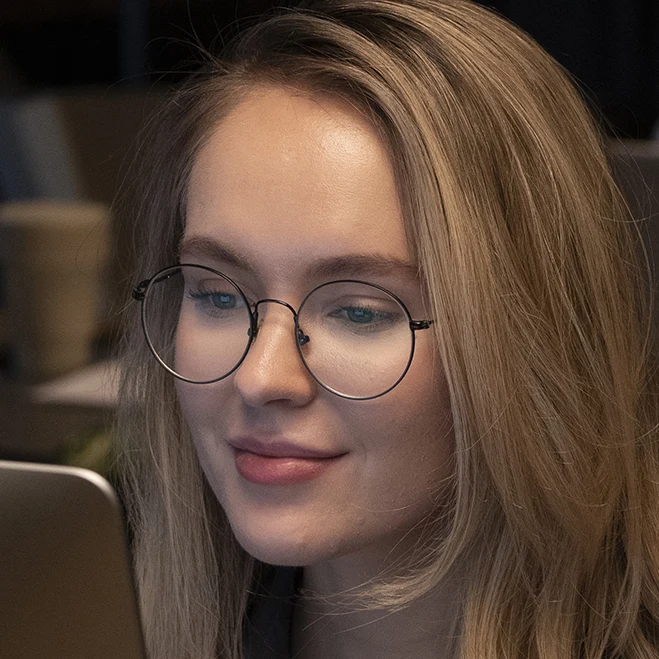
Eliza Miller
March 21, 2025
In aerospace and defense systems – whether a satellite, a fighter jet’s avionics, or a rugged drone – the phrase “mission-critical” is no exaggeration. In such systems, power management modules (PMMs) are the lifeline that ensures every electronic component receives stable, reliable power under all conditions. A failure in the power supply can cripple an entire mission: imagine a spacecraft resetting because of a power glitch or a radar going dark due to a failed voltage regulator. For this reason, high-reliability power electronics are treated as foundational elements in design, often with as much scrutiny as the processors and sensors they support. “Without a resilient electronics supply chain, there is no resilient defense sector,” noted one industry report, emphasising that even the fanciest payload is useless if you can’t power it. Here, we explore why power management is so critical and how modern technology is addressing the unique challenges in this domain.
The Backbone of Reliability
Mission-critical power modules must deliver consistent, clean power in harsh environments. Unlike a desktop gadget plugged into a stable outlet, these modules face wide input voltage swings, extreme temperatures, shock/vibration, and sometimes radiation. For example, an aircraft power bus can fluctuate (per MIL-STD-704, an aircraft’s DC bus might drop or surge due to engine start, etc.), and the power unit must maintain a steady output voltage to sensitive electronics throughout those transients. In space, solar arrays output and battery levels vary widely between eclipse and sunlight periods, yet satellite instruments require tight voltage regulation. Furthermore, once a satellite or deep-space probe is launched, maintenance or replacement is impossible – the power system must work flawlessly for years or even decades. This drives incredibly rigorous design and testing protocols. Radiation-hardened components (resistant to single-event upsets and total dose effects) are used for space power modules, and they undergo exhaustive life testing. As an example, Infineon’s IR HiRel division highlights that their space-grade power MOSFETs are tested to survive 30 krad total dose and high-energy particle strikes without performance loss.
Even in terrestrial military applications, power supplies are tested against standards like MIL-STD-810 (environmental conditions: temperature extremes, shock, humidity, etc.) and MIL-STD-461 (electromagnetic interference/compatibility) to ensure they won’t falter under combat conditions. The fact that many high-reliability power modules are specified for operations from –40°C to +85°C (or broader) indicates the extremes they handle. In fast jets, these modules might see high G-forces; in armored vehicles, they endure continuous vibration. Thus, robust mechanical design (e.g., secure component mounting, vibration damping potting) and electrical design (handling input surges, output short-circuits, etc.) are imperative. A key consideration is managing transients: for instance, when a radar transmitter pulses on, it draws a huge surge of current. The power module must not only source that current but do so without letting the output voltage dip outside the allowed range. Techniques like large output capacitors, “soft start” circuits, and transient suppressors are employed.
High reliability also means often having redundant power pathways or graceful degradation. In mission-critical designs, there might be two parallel power supplies load-sharing; if one fails, the other seamlessly takes over. Or a spacecraft might have multiple power “strings” so that a failure in one solar array/regulator chain doesn’t doom the mission. These redundancies have to be carefully managed to avoid interference or instability (for example, two supplies driving one bus can oscillate unless properly balanced).
Advanced Components for Efficiency and Performance
Traditionally, power electronics in aerospace/defense used silicon-based devices (MOSFETs, diodes) designed for robustness more than efficiency. Today, there’s a strong push to incorporate wide-bandgap semiconductors like GaN and Silicon Carbide (SiC) into power modules. The same GaN that helps RF amplifiers is also a boon for power conversion: GaN transistors can switch at much higher frequencies with lower losses, enabling smaller and lighter converters. This is crucial in weight-sensitive applications like aircraft and spacecraft. By switching faster, the inductors and capacitors in a DC-DC converter can be much smaller. Higher efficiency also means less heat to dissipate, which is always a limiting factor in sealed, compact electronic bays. A cooler, more efficient power module directly improves reliability (since thermal stress is a major cause of electronic failures). We see products now like 1kW DC/DC converters in brick form factors using SiC transistors to achieve 95%+ efficiency where older designs might be 85%. Less wasted energy also means, in something like an electric drone, more battery life or in a satellite, less precious energy lost from the solar supply.
However, introducing new tech like GaN must be done with caution in mission-critical contexts. These components undergo extensive burn-in and some designers will derate them significantly (using them well below their maximum ratings) to ensure longevity. Companies like Vicor, Crane Aerospace, and others have developed COTS components adapted for mil/aero – offering modular power converters that meet military standards for input, output, and ruggedness. For example, a “plug and play” 28V to 5V converter that meets MIL-STD-704 (aircraft 28V bus characteristics) and MIL-STD-1275 (ground vehicle power) will save a lot of custom design effort while still providing the needed reliability.
Another innovation area is digital power management. Contemporary power modules may include digital control loops and telemetry. This allows for things like real-time health monitoring of the power system (reporting voltages, currents, temperatures to a central maintenance system) and even dynamic reconfiguration. In a satellite, for example, a digital power controller could optimally re-distribute load between multiple converters to balance temperatures, or shed non-critical loads if available power drops (say, due to a solar array issue). Essentially, power modules themselves are getting smarter, not just delivering juice but communicating and adjusting as part of an integrated system management approach.
Why “Clean” Power Matters for Mission Systems
It’s worth highlighting that mission electronics often include sensitive sensors and communication gear that can be disrupted by noisy power supplies. A poorly designed power module that injects ripple or switching noise could degrade a satellite’s sensor readings or a military radio’s performance. Thus, high-reliability PMMs put a premium on power quality: low ripple, low electromagnetic emissions, fast transient response. For instance, a radar’s receiver might require its supply to have microvolt-level noise floors, otherwise spurious tones could appear in the RF spectrum. That drives the use of filters, shielding, and sometimes linear regulation stages after the main converter for ultra-sensitive circuits.
In aerospace, electromagnetic interference (EMI) control is tightly regulated. The power module is often one of the largest sources of EMI (due to high-frequency switching), so designers incorporate advanced filtering on both input and output. Meeting MIL-STD-461 for EMI means the module’s noise stays below certain microvolt/milliwatt levels across various frequency bands. This ensures, for example, that the aircraft’s power system won’t interfere with its own radio or navigation signals. Achieving this often means additional chokes, EMI filters, or synchronisation of switching frequencies to avoid beats.
Case Study: Satellite Power Management
Consider a satellite’s payload module – it might have a PMM taking unregulated bus power (around 50–100 V from solar arrays/batteries) and converting it to multiple voltages: 12V for mechanical components, 5V and 3.3V for digital electronics, maybe ±15V for analog amplifiers, etc. This PMM must operate through eclipses (battery discharge) and solar charging (when bus voltage varies). It must tolerate radiation, as mentioned, and manage energy efficiency closely because every watt saved is either additional instrument operation or reduced thermal load. According to an EE Times interview, for electric propulsion and other high-voltage satellite needs, converters must handle up to 600 V and provide consistent power conversion over long missions. They also mention the need to handle transients and maintain constant output despite input changes. Companies have developed specialised radiation-tolerant DC-DC converters that meet these needs, with features like magnetic feedback (which can be more rad-hard than optical feedback), single-event latchup protection, etc.
The satellite example highlights a general principle: design margin. Mission-critical power systems are usually designed with ample margin – components rated far above normal operating points, ability to handle worst-case scenarios like load dump or short circuits without damage. If a critical avionics box draws more current than expected (perhaps due to new software or a partial failure elsewhere), the power supply should ideally handle it rather than shut down. This is why many military power units are oversized relative to average load.
Ensuring Strategic Autonomy and Supply Security
Finally, there is a broader strategic angle to power modules: they are often subject to export controls and supply chain risk. Many countries consider radiation-hardened or military-grade power electronics as strategic items. For European defense projects, for instance, relying on a foreign supplier for a tiny but crucial power controller chip could be a security vulnerability. This concern ties into the larger push for strategic autonomy in semiconductors (as with the EU Chips Act), which includes the analog and power domain. In fact, Europe’s share of the global electronics manufacturing (which includes power components) has dropped sharply, raising alarms about security of supply. Thus, there’s interest in bolstering domestic capability in high-reliability power modules too, ensuring local industries can build the power solutions needed for European satellites, aircraft, and military platforms without bottlenecks.
In conclusion, power management modules may not receive the fanfare of a new processor or sensor, but they are truly the unsung heroes of mission-critical systems. They embody engineering for reliability: built to absorb the stress so that the rest of the system can operate smoothly. As the saying goes in engineering circles, “The power supply is often the first to fail,” which is why in aerospace and defense, extraordinary measures are taken to prevent that from happening. By leveraging robust designs, advanced materials like GaN, and rigorous testing, modern PMMs achieve phenomenal reliability records – many satellites have flown for decades without a single power hiccup. They enable high-performance electronics to function in the most unforgiving conditions, from deep space to the heat of battle. Every time a mission succeeds under duress – a surveillance drone stays aloft hours longer or a spacecraft travels billions of miles – there is likely a quietly efficient power module to thank, diligently doing its job of keeping the electrons flowing, come hell or high water.
Sign up for expert insights on cutting-edge technology
Stay informed on innovations that power the future, directly from our team to your inbox.